
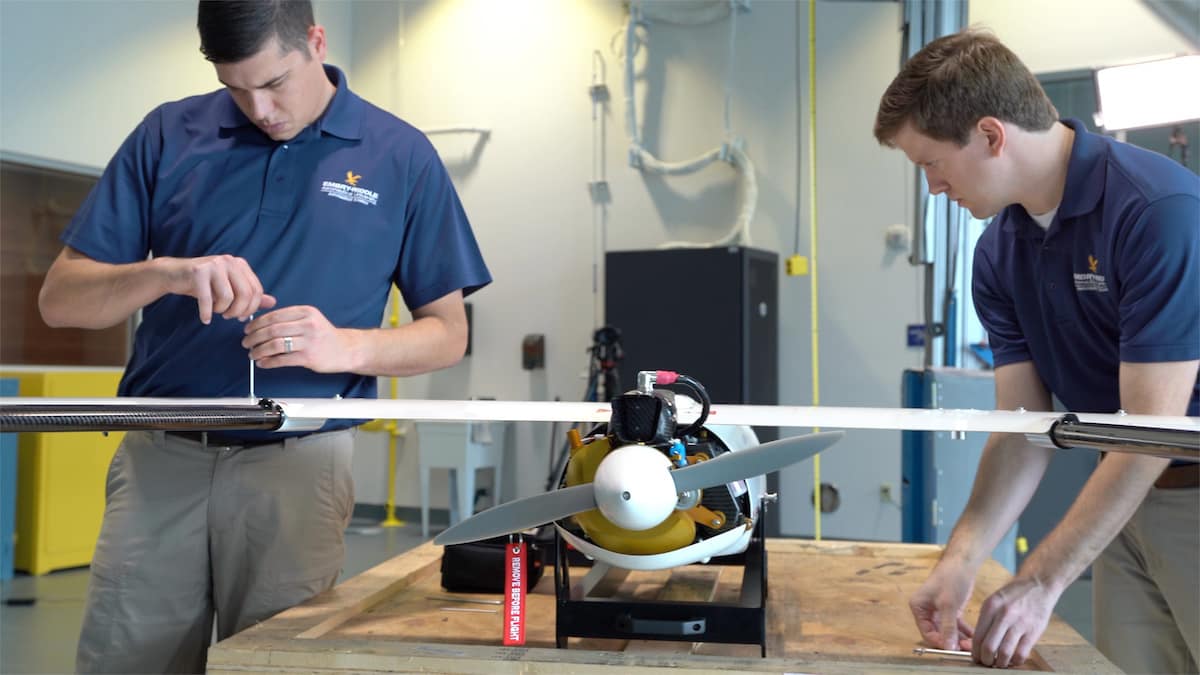
You must temper the technician's approach with fiscal responsibility. However, the technician probably does not have the broader perspective that you have. Generally, if a part is required, the technician wants it immediately and rightfully so, as that is the technician's primary responsibility. How much inventory with its related costs is the question that requires your attention as the manager of inventory.Ī technician's responsibility is to complete the maintenance work as quickly as possible. As we have discussed, inventory is a necessary asset for the organization to meet the maintenance department's overall objective for aircraft availability. In other words, what can you do to control your inventory and its associated costs? The ideas listed below do not include everything that you may want to try, but they should give you a good start as you develop your specific plans and ideas. Techniques for managing or controlling inventory So if you are one of the lucky managers who has inventory as part of your domain, what can you do when it comes to controlling and managing this critical but potentially expensive asset within your organization? While you should not consider this an insult, various sources indicate that the average maintenance manager comes from a technical background, which is a background that focuses on maintaining aircraft, not necessarily controlling inventory. Accomplishing that can prove difficult for the maintenance manager. In essence, the maintenance organization needs to have the right part available at the right time, and if the responsibility for inventory falls upon the maintenance manager, a reasonable cost is added to the equation. Therefore, a balance is required when it comes to inventory as the maintenance organization strives to reach its objective concerning aircraft availability. Regardless of whether or not they're obvious, costs consume an organization's limited resources. insurance, taxes, storage, obsolescence). Some costs are obvious, such as the actual purchase price of an item, while others are not so obvious, such as the costs associated with carrying inventory (e.g. Unfortunately, inventory comes with a cost.
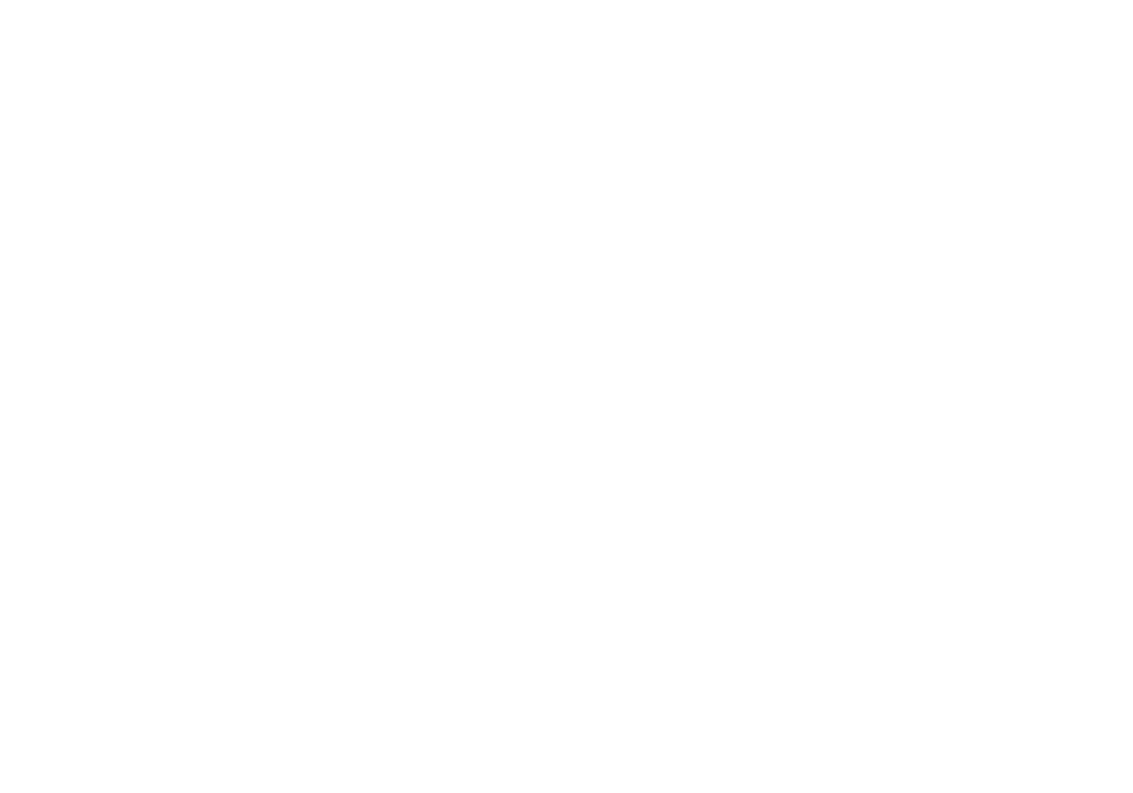
All of these factors can have an effect on the level of inventory required in your organization. Those factors could include dealing with an inefficient vendor, predicting the timing of a part's failure, having multiple operational locations, competing objectives of internal departments, preparing for the effect of bulletins and directives, and many other reasons that you probably know better than I do. Other factors can complicate the maintenance organization's ability to meet its objective of having the right part available at the right time. Therefore, due to the nature of, or imperfections in, the supply and demand chain, maintenance organizations are forced to carry inventory. To meet that objective, the maintenance organization must have parts available when needed. In maintenance organizations, one of the most basic objectives is to have aircraft available when required by flight operations.
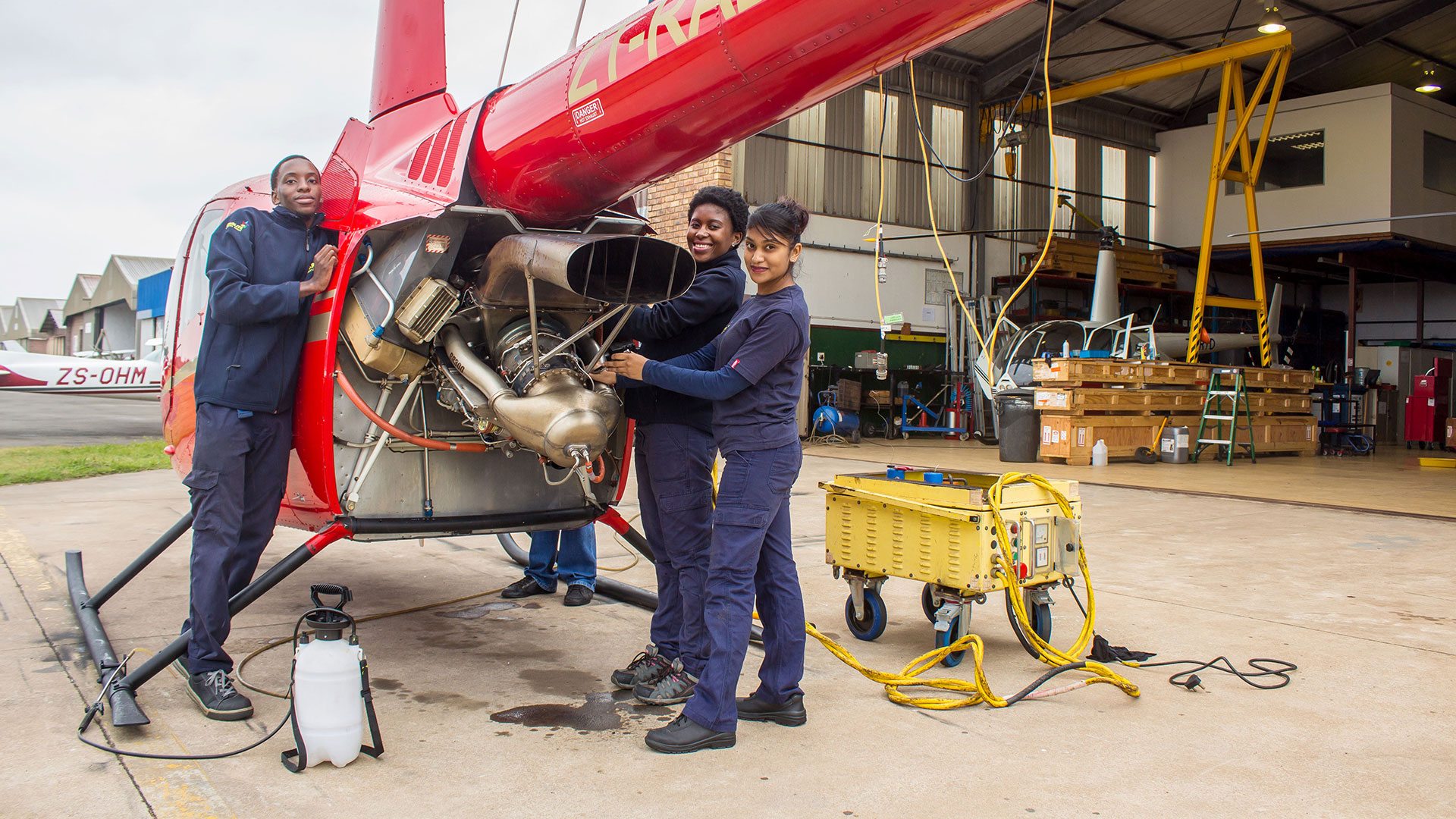
#FLIGHT SCHOOL INVENTORY MAINTENANCE MANAGMENT SERIES#
More specifically, the second part of this series will explore the answers to a fourth question. What are the costs associated with inventory?īut if the information stopped there, I would be leaving out another important item associated with inventory, control.What factors can influence the levels of inventory?.The first article answered three questions. The purpose of the first article of this two-part series on inventory (April's online feature) was to eliminate some of the irrational emotions concerning inventory by gaining a better understanding about the cause and nature of inventory. Whether you want it or not, some amount of inventory is necessary for every maintenance organization.
